Virtual Design + Construction Services
Model-Based Estimating
Juneau is preconstruction-focused and the integration of VDC and preconstruction provide a synergistic approach to estimation especially in the conceptual phase. Our in-house model development allows for quick adaption to changes in design; via cost loaded models and model-based quantification. We can demonstrate solutions for constructability and value engineering based on our experience and in-house systems engineering support.
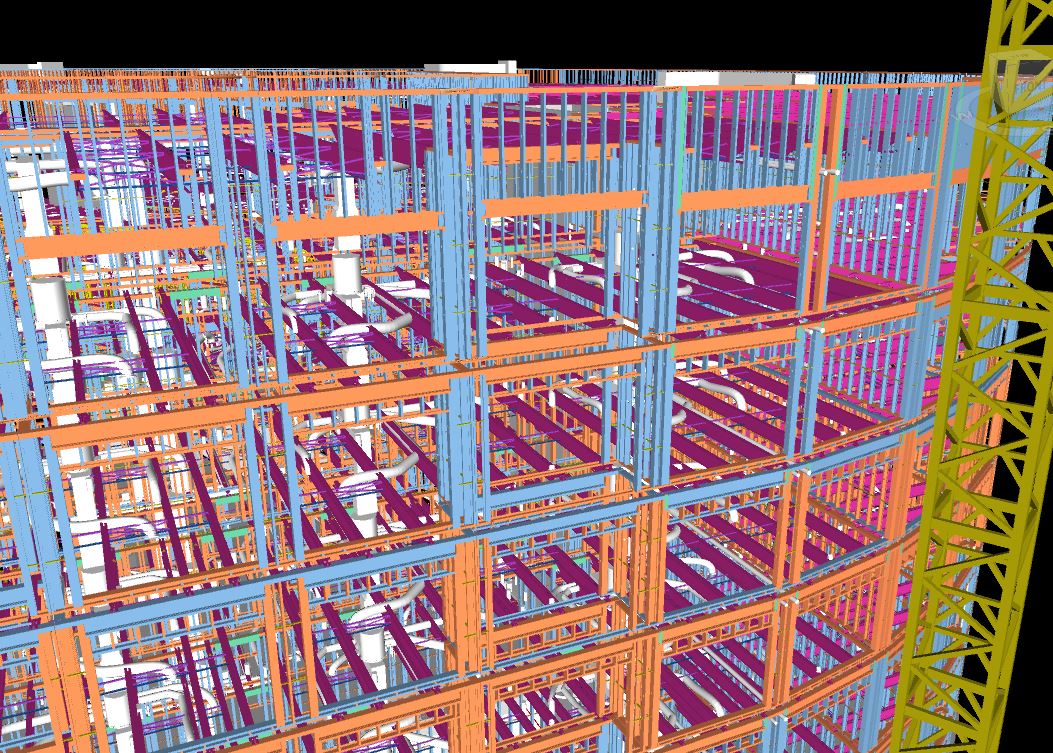
Systems Coordination
Juneau develops BIM coordination plans and executes them on every project. The key to a successful BIM coordination effort is early team buy-in and a “just the right amount” of BIM approach for each project. Our in-house modeling combined with trade partner modeling produces accurate and through models. This approach allows for systems coordination prior to construction, ultimately increasing construction productivity and safety.
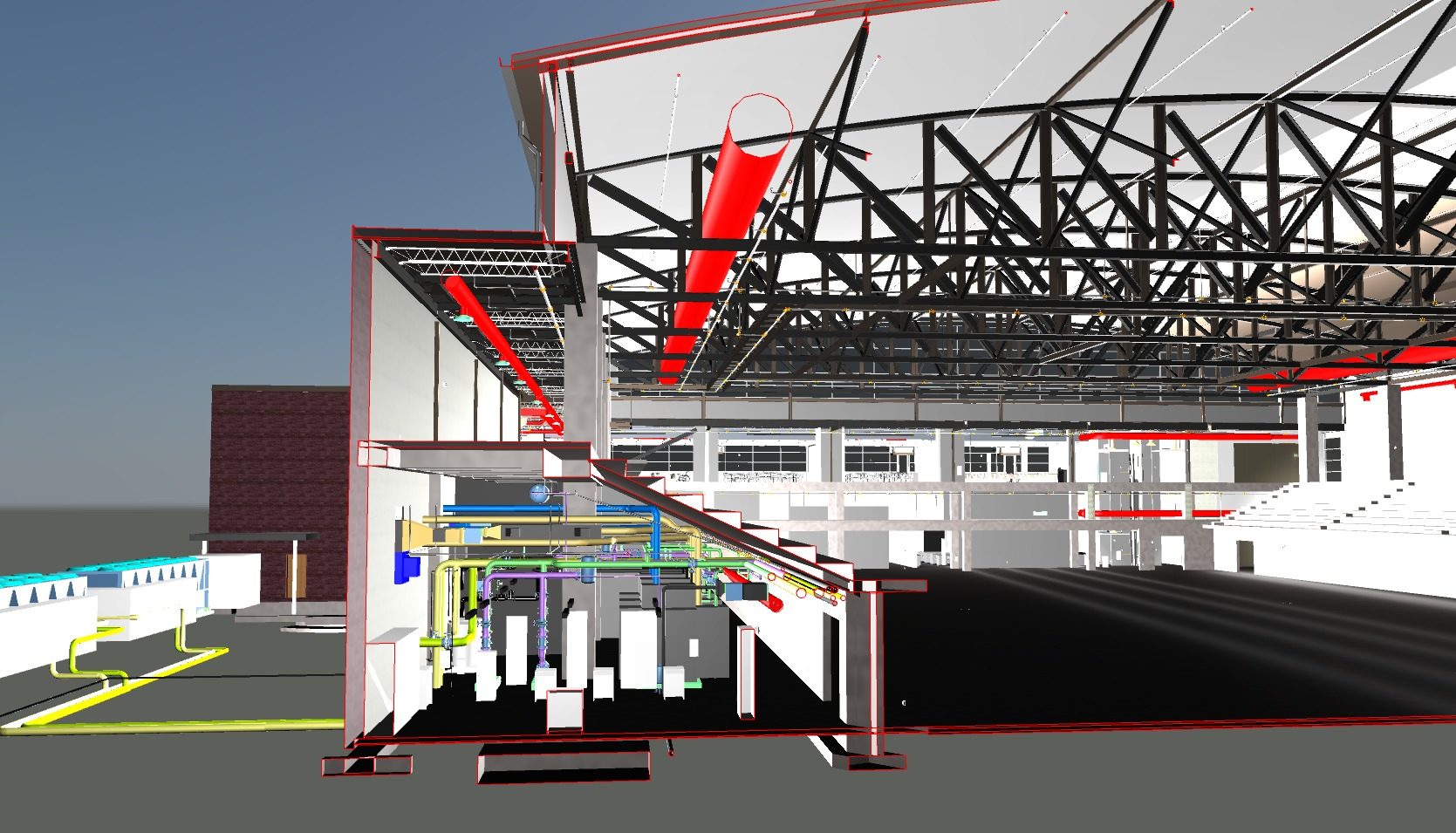
Site Logistics
At Juneau, our Preconstruction, Operations, and VDC departments work together to ensure the safety of all those involved in and around the jobsite. A clear site logistics plan is created during the preconstruction phase of the project to reflect crane locations and travel paths (if applicable), delivery routes, on-site parking, laydown areas, and jobsite boundaries. An effective plan will ensure safety on the jobsite and efficient workflows throughout the course of the project.
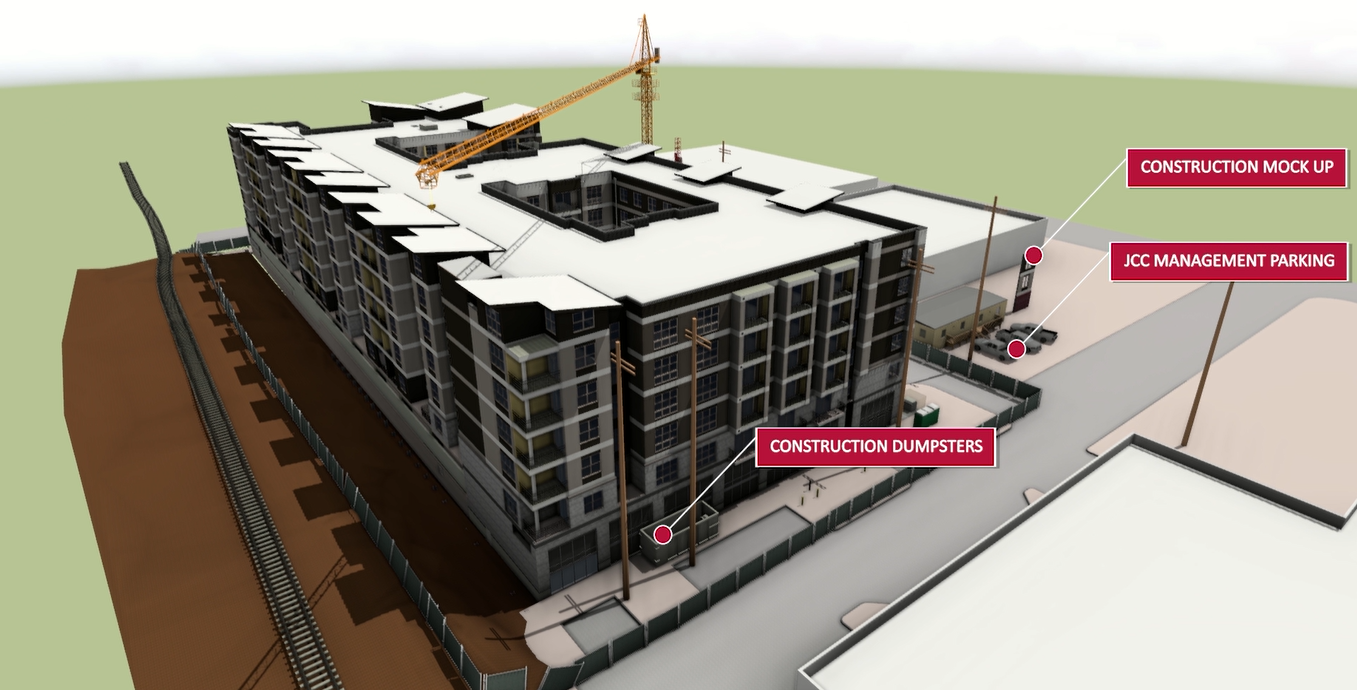
Mixed Realities
Juneau uses Virtual Reality (VR) Augment Reality (AR) with our project teams, engineers, architects, trade partners, and Owners to gain a better insight of the construction process. Mixed Reality is everything from a simple technique that can be utilized with a QR code and smartphone to a full immersive experience designed to simulate finish conditions.
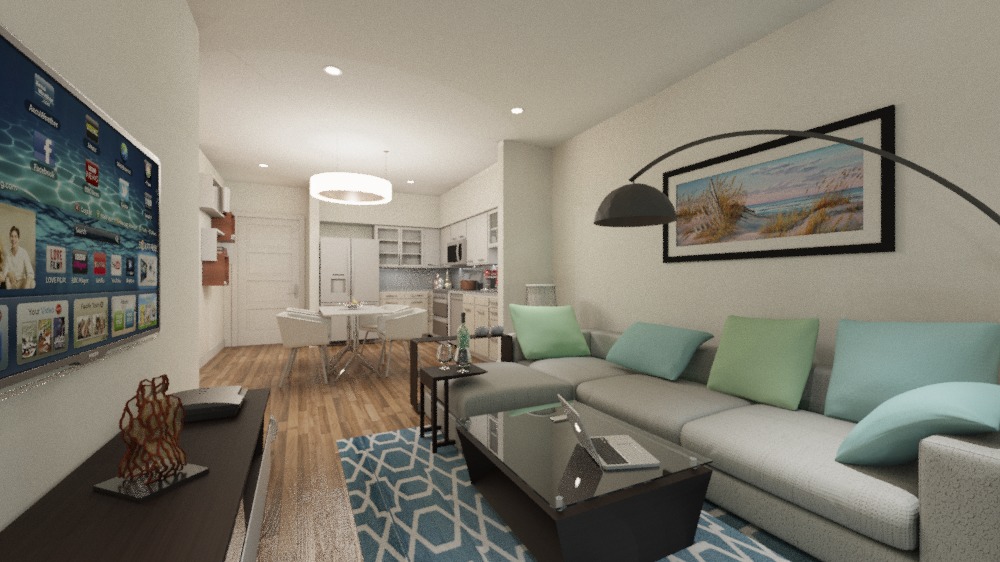
Unmanned Aircraft Systems
Juneau is prepared with a fleet of unmanned aircraft systems (also known as drones) to provide more detailed information about the site, structure, and envelope throughout all stages of the project. Drone documentation can provide everything from quality assurance for envelope inspections to enhancing the overall experience for the Owner during construction, especially when used in conjunction with OAC meetings. Drones are a simple, but powerful tool, and one of the most efficient ways to document construction progress.
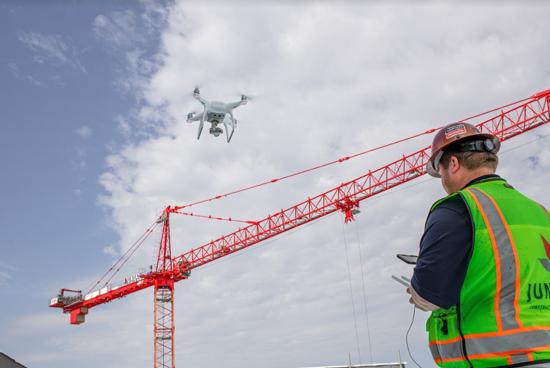
4D Modeling
Juneau uses 4D modeling to assist with schedule development and analysis. The combining of 3D models with schedule data allows us to simulate the construction process. Our 4D simulations combined with our vast industry experience over multiple market sectors allows efficient and creative schedule development.
Laser Scanning
Juneau Construction Company uses laser scanning technology in coordination with Building Information Models (BIM) to plan and verify projects. The laser scanner gathers millions of points to create a point cloud of data for a project. The point cloud is used to verify and determine a vast amount of information about a project, from MEP coordination, to structural analysis, and existing condition surveys.
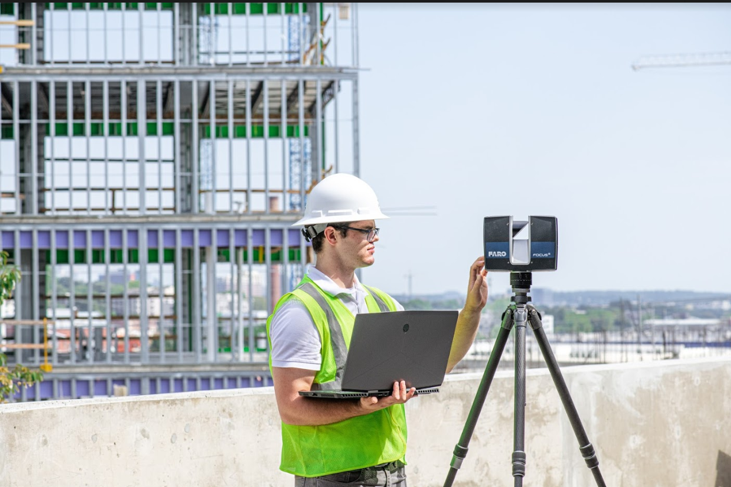
Model-Based Layouts
Juneau uses layout points generated within BIM to layout the building geometry on the jobsite. This ensures the most accurate information is being utilized in the field.
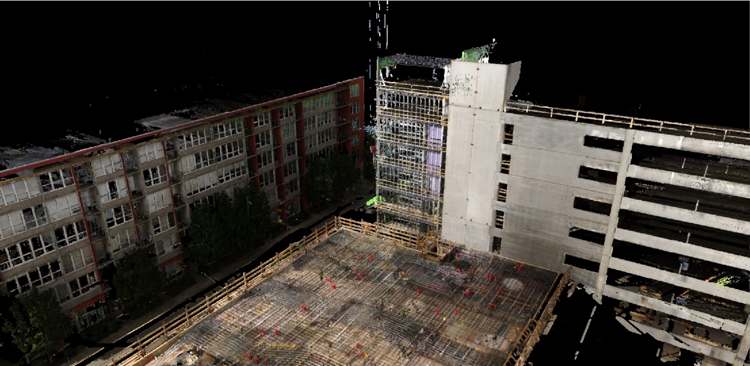
Safety
Juneau uses 4D scheduling and advanced site logistics models to develop project specific safety plans. Our safety plans analyze worker density, pinch points, and fall hazards among the many other variables also evaluated prior to the start of construction. The 3D approach to site development and safety help to visualize a project holistically to provide better results.
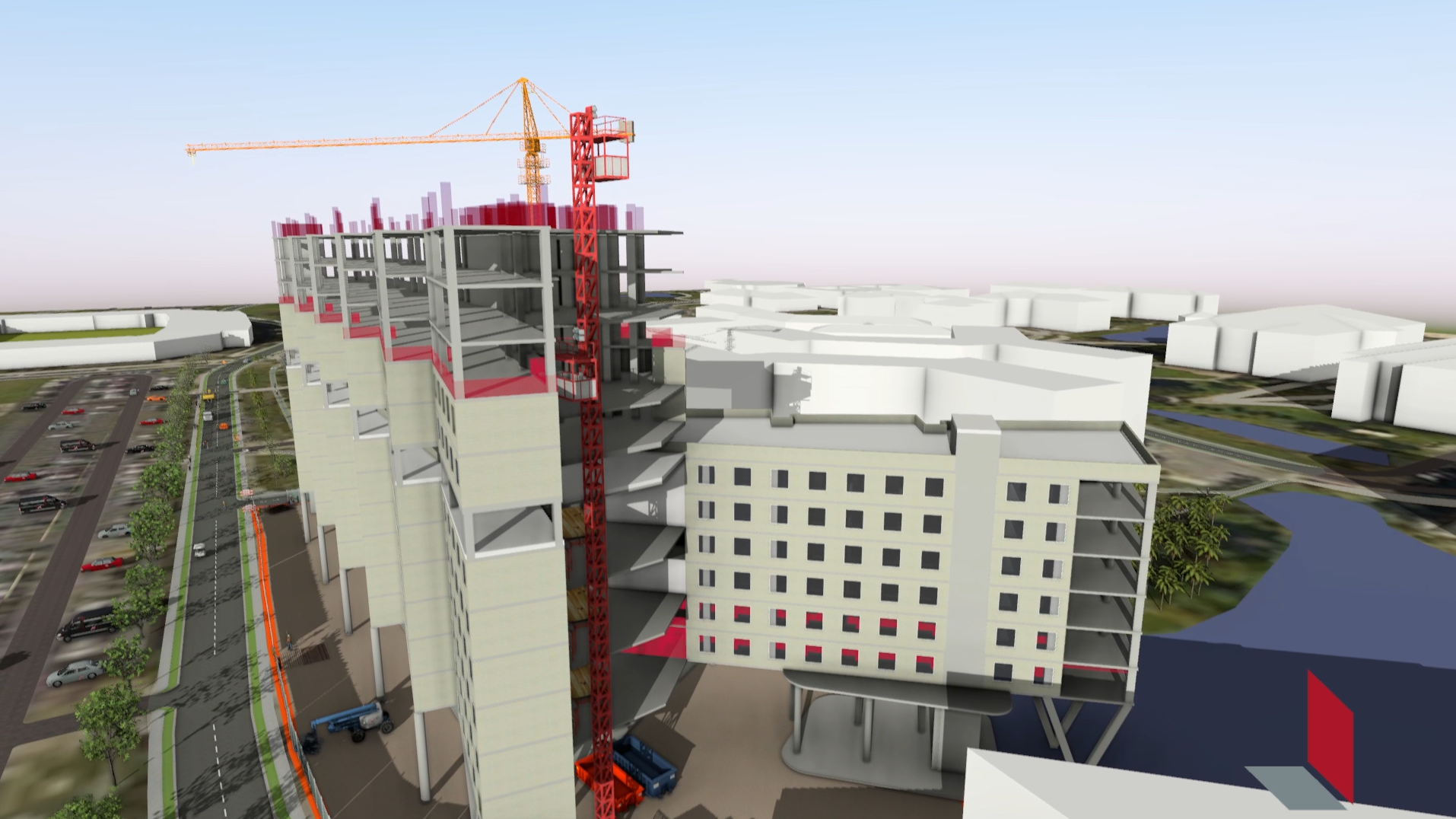
Virtual Design and Construction (VD+C) is the use of coordinated multi-disciplinary 3D models to convey overall construction intent of a project. This allows us to build your project virtually before we ever step foot onsite.
VD+C is different than Building Information Modeling (BIM). Both utilize the same coordinated 3D model for different end goals. The BIM is a collaborative model of designed elements emphasizing the aesthetic design. While VDC utilizes the existing BIM to digitally construct the project.
BIM and VD+C are essentially tools that the AEC teams use to better communicate the design intent and the construction process. This leads to reduced overall time and cost on a project.
VD+C aims to improve communication through the visual medium. This leads to effective team collaboration bringing together various disciplines into a shared model. These models are linked so that they all can access shared data, and if a user highlights or changes an aspect of one, the integrated models can highlight or change the dependent pieces of the coordinated model. The models are multi-disciplinary in the sense that they represent the Architect, Engineers, Contractor (AEC), and Owner of the project, as it moves to VD+C, the model will incorporate the various sub disciplines.
VD+C helps use new and emerging technology to empower the construction process. BIM help visually communicate the construction means and methods and streamlines the fabrication process. They are used to coordinate subcontractors’ work into a cohesive model and can be used as a tool to visual construction scheduling. This aids the build sequencing and material and delivery staging on the job site. Robotic digital layouts can be linked back to the coordinated model reducing necessary field staff. Lastly, quantity take offs can be done from models to verify in-house estimating figures.
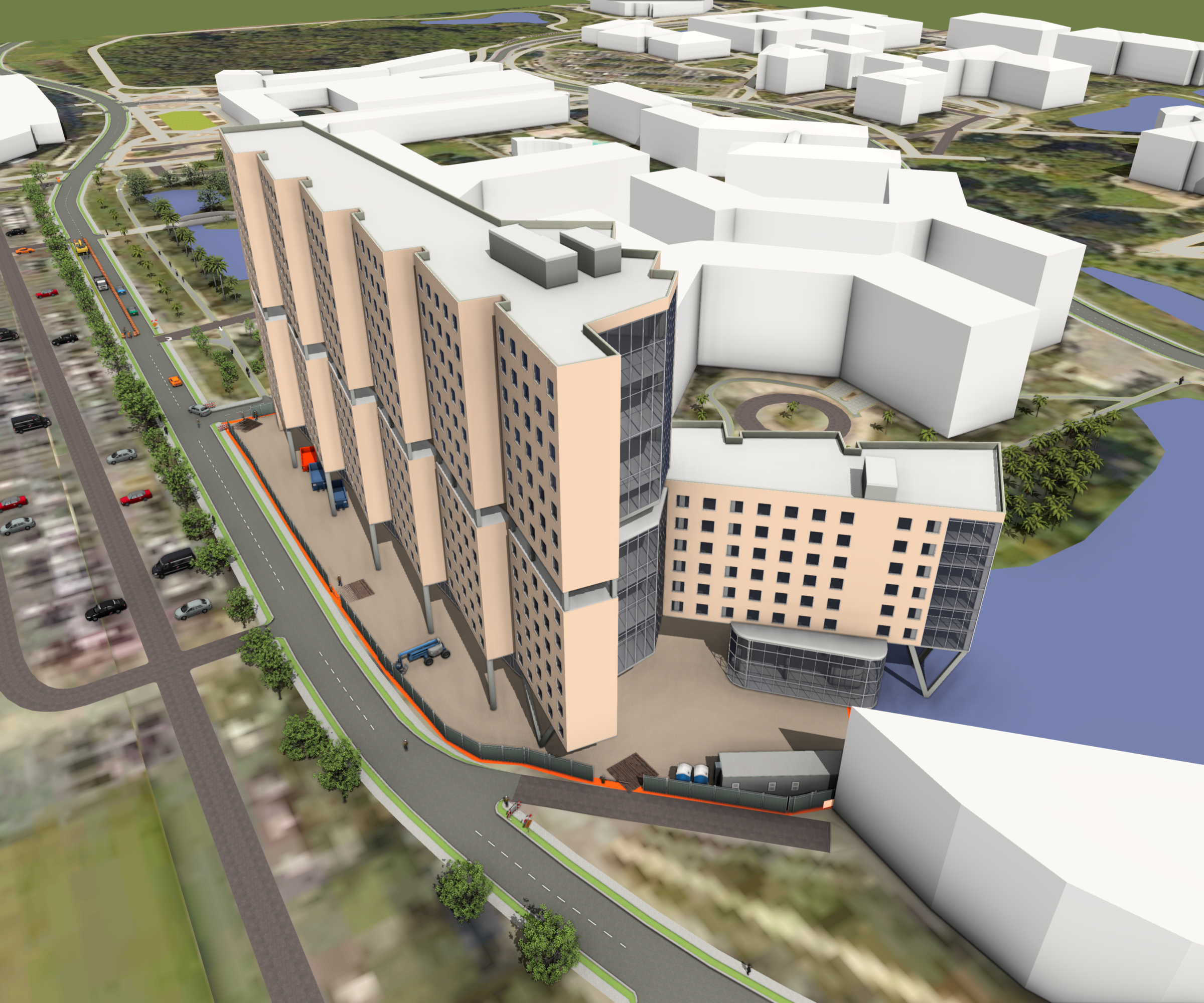
Utilizing BIM and Revit for Cost Estimation
BIM and Revit are both powerful and predictable tools to provide accurate quantification during the cost estimation phase.
Learn More